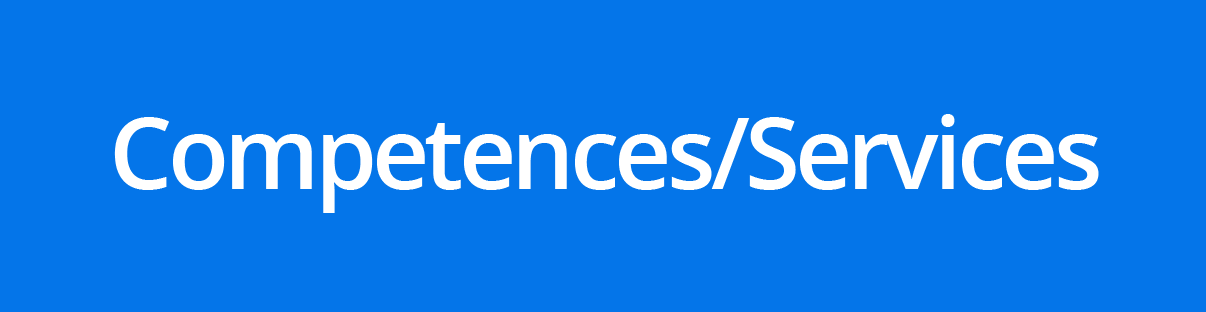
Engineering
Our engineering department has an experience for decades in the engineering and design of demanding and complex pressure vessels. The preparation of detailed fabrication drawings, strength calculations, statics etc., based on various rules and client specifications, for us go without saying. For our engineering up-to-date CAD equipment and calculation programmes are available. Among other things the following software is used:
⦁ Inventor (3D models)
⦁ AutoCAD
⦁ DIMy
⦁ NozzlePro
⦁ PV Elite
⦁ FEM for special applications
⦁ Various proprietory programmes for special calculation demands
Rules:
⦁ AD-2000
⦁ EN 13445
⦁ ASME Sec. VIII Div.1 & Div.2
⦁ China requirements
⦁ Stoomwezen Rules
⦁ BS 5500
⦁ TEMA
⦁ EN 1090
⦁ PED
Fabrication
Our production plants and transportation facilities are dimensioned even for apparatus with very large dimensions and weights. For this there are production halls with 20.000 m² and company grounds of 50.000 m² available.
Fabrication capacities:
length: 85 m
diameter: 12 m
plate thickness: 150 mm
weight: 1000 t
heat treatment furnace: mobile construction (no size limitation)
Materials
The range of the processed material qualities has continously increased over the last years. Besides the common carbon and stainless steels many new materials in special qualities have been added. This mainly concerns premium chromium and nickel alloys as well as clad material qualities. These comply in a special way to the client requirements for a better and better corrosion resistance, wear resistance and tensile strength, also at high temperatures. What makes the value of the new steel qualities is also the combination of these properties. Among others we do process the following materials:
*carbon steels
– steels for hydrogen service at elevated temperatures and pressures – high-temperature and creep-resistant steels
– tempering steels
– general-purpose constructional steels
– fine-grained construction steels (high and low temperature, HIC resistant)
* stainless steels
– ferritic
– austenitic
– martensitic
– superaustenitic
– duplex
– super-duplex
* nickel and nickel alloys
* clad materials (rolled clad and explosion clad)
The a.m. materials are processed in accordance with the relevant EN standards and other international rules, such as e.g. ASME, British Standard.
Our welding department watches the development of new material grades very intensely. In collaboration with our suppliers for steels and weld filler materials we perform weld tests and evaluate these in our own laboratory, based on corresponding directives for processing are determined.
Welding
Welding plays a centrol role in our fabrication. The welding processes are thus continuously tested and optimized. Currently the following weld procedures are used:
⦁ SMAW
⦁ GMAW / SAW
⦁ SAW
⦁ RES welding (up to 2500 A)
⦁ GTAW
⦁ GTAW orbital (tube-to-tube)
⦁ GTAW orbital (tube-to-tubesheet)
⦁ WIG orbital (tube behind tubesheet, gap-free)
One particularity in our welding is cladding / weld overlay. With our proprietary developments it is possible to clad tubes with an internal diameter of 40 mm on a length of 2 m. Of course, also considerably larger dimensions are possible.
We have already cladded shell courses with a diameter of 8,5 m by means of electroslag procedure. In addition to austenitic CrNi-alloys also Ni-based-alloys and wear-resistant weld overlay are processed by us as cladding material.
Testing
We do have our own testing department with experienced test personnel, certified in accordance with DIN EN ISO 9712, level 2 and 3, PED and ASNT-TC-1a level II and III. Among others the following test procedures are used:
⦁ RT
⦁ UT
⦁ PT
⦁ MT
⦁ PMI
⦁ helium leak test
⦁ TOFD
⦁ phased array
Moreover we execute destructive tests in our shop laboratory. These include the following tests:
⦁ impact test
⦁ tensile test (up to 600 kN)
⦁ technological bending test
⦁ hardness test
⦁ micrographic test
Our machines for the destructive tests are mainly used for procedural tests and work tests. For exceeding tests we cooperate with accredited test laboratories.
Surfaces
The surface treatment is done on our company yard. By means of mobile halls it is possible for us also to coat very large component parts under controlled conditions. The following procedures are regularly used by us.
⦁ blasting with steel shot or glas beads
⦁ painting and corrosion protection coatings
⦁ corrosion protection coatings
⦁ fireproofing
⦁ pickling and passivation
⦁ TSA (thermal spray aluminium) coatings
⦁ lining
⦁ electropolishing
The preparation of corresponding procedures and the performance of the required tests during the execution phase for us go without saying.
Dressing
Upon request the columns are prepared in our works to be ready for erection (fully dressed) The apparatus can also be supplied complete with platforms, ladders, insulation, pipings, instruments for measuring and controlling, assembled internals and electrical systems. The apparatus then only have to erected and conntected to the points of intersection at site.
Transportation
Our plant components are destined for locations on all continents. Upon request we arrange for the entire transportation from our works in Kleve to the point of destination in our responsibily, regardless of the means of transportation and including all permits.
In some cases the vessels and apparatus fabricated by us are transported by means of special vehicles on the road. In case of very large dimensions, however, the transportation is done via ship. Our works is located in the vicinity of the river Rhine and sea port Emmerich. Via river Rhine also international ports, such as Rotterdam or Antwerp can be easily reached. From here a possible shipment to overseas is done.
Assembly
Usually our columns and vessels are delivered to their final destination as completed component parts, even in case of very large dimensions.
Only as an exception it is necessary to deliver columns and vessels to site in several parts and to weld the components prefabricated in the shop as far as possible together on site. This procedure is of significance when the existing transport routes do not allow for a delivery of a complete apparatus. For these cases qualified assembly personnel and complete site equipment is available. In case of need we can submit a detailed assembly concept already in the enquiry stage. For this we can revert to extensive experience; we have already assembled columns with a unit weight of 600 t in component parts at site. This can be a of a high interest, if site-internal pipings prohibit the lifting of large apparatus as a whole across supply lines, however, individual parts can be shipped below the pipings. In case of need, we can, of course, also do the dismantling and disposal of the existing plant components.
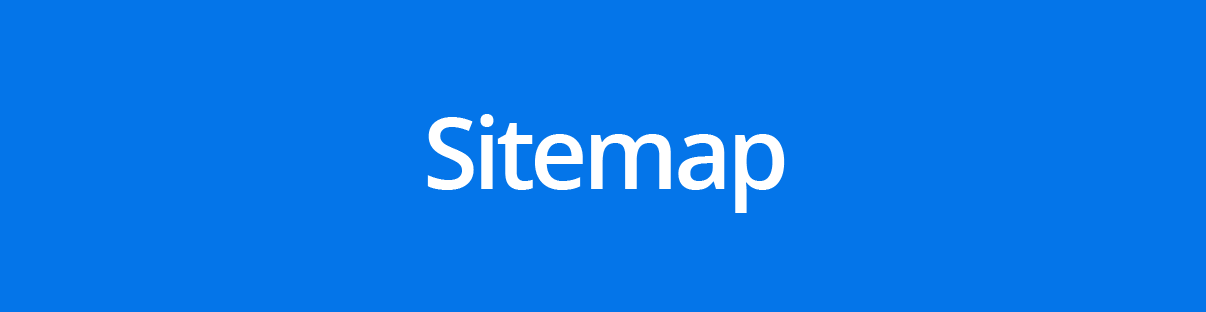
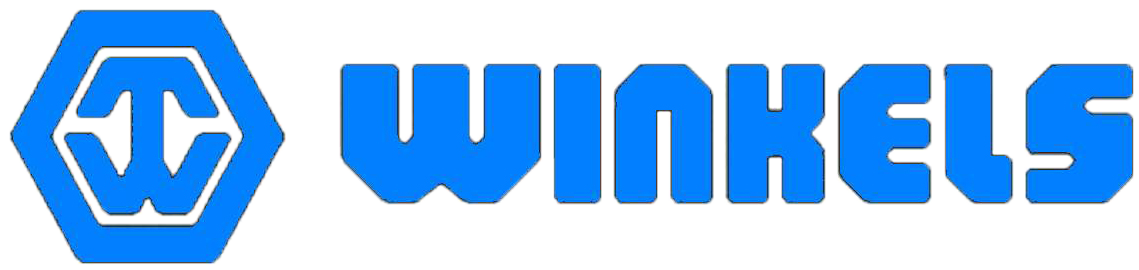